China's Leading Speaker Manufacturer Revealed: The Rise of Manufacturing
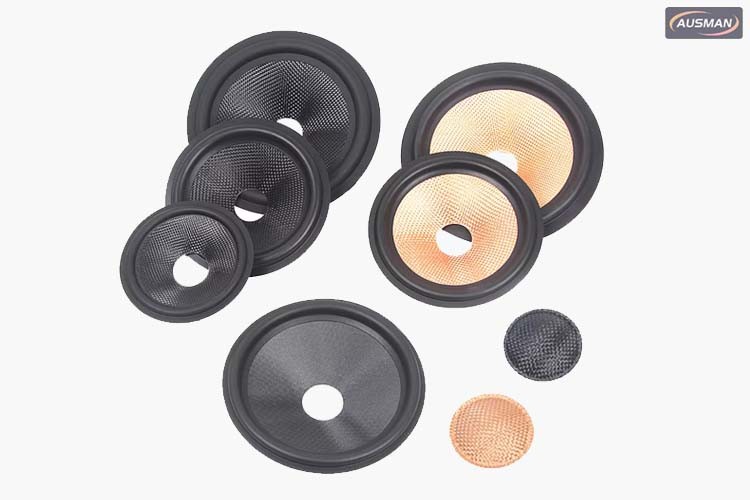
Speaker Glass Fiber Cones
Overview
From the evolution of speaker cone materials to innovative manufacturing technologies, here we discuss the speaker cones from all aspects, including raw materials, types, manufacturing processes, development directions and prices.
Contents
1. Introduction to Speaker Cone Manufacturing
2. History of Speaker Cone Manufacturing
3. Key Components of Speaker Cones
4. Speaker Cone Manufacturing Process
5. Types of Speaker Cone Technologies
6. Quality Control in Speaker Cone Production
7. Innovations in Speaker Cone Manufacturing
8. Environmental Considerations
9. Challenges and Solutions
10. Applications of Speaker Cones
11. Impact of Speaker Cone Design on Sound Quality
12. Manufacturers of Speaker Cones
13. Future Trends in Speaker Cone Manufacturing
14. Packaging and Shipping of Speaker Cones
15. Conclusion
16. FAQs
1. Introduction to Speaker Cone Manufacturing
What Is A Speaker Cone?
A speaker cone is a crucial component of audio systems, serving as the primary surface that vibrates to generate sound when driven by an electrical signal.
It is typically made of materials such as paper, polypropylene, kevlar, or aluminum and plays a pivotal role in sound reproduction.
How It Works
The vibration of the sound cone causes the surrounding air to vibrate, producing sound waves, thereby emitting sound.
Importance of Speaker Cones in Sound Production
Speaker cones are essential in sound production as they are responsible for transforming electrical signals into audible sound waves.
The design and material composition of speaker cones significantly influence the quality and characteristics of the sound produced, making them indispensable components in audio systems.
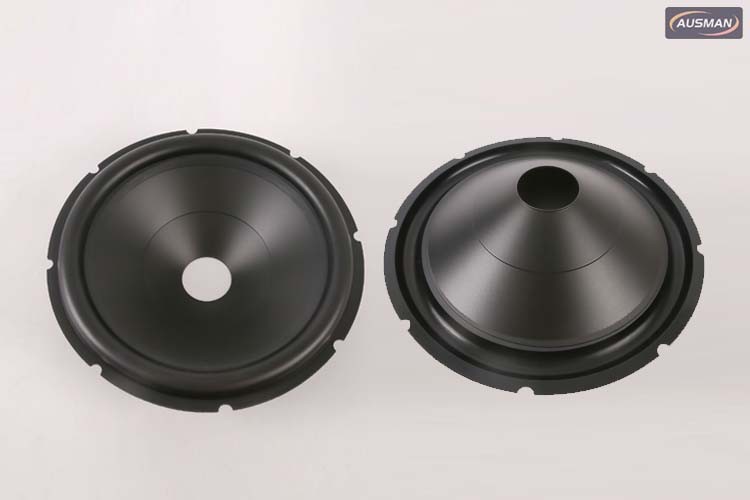
10 Inch Speaker Paper Cone
2. History of Speaker Cone Manufacturing
Evolution of Speaker Cone Materials
The history of speaker cone manufacturing has witnessed significant advancements in materials. From the early days of paper cones to modern materials like polypropylene, kevlar, and aluminum, manufacturers have continuously innovated to improve sound quality and durability.
Milestones in Speaker Cone Technology
Milestones in speaker cone technology include the development of advanced molding techniques, improvements in material science, and innovations in cone design.
These milestones have led to the diverse range of speaker cone technologies available today, each offering unique sonic profiles and performance attributes.
3. Key Components of Speaker Cones
Materials Used in Speaker Cone Manufacturing
Common materials used in speaker cone manufacturing include paper, known for its natural sound reproduction; polypropylene, prized for its lightweight and rigid properties; kevlar, valued for its exceptional strength-to-weight ratio; and aluminum, renowned for its excellent transient response and high-frequency extension.
Design Considerations for Optimal Performance
Design considerations such as cone shape, size, and construction are crucial for achieving optimal performance in speaker cones.
Factors like frequency response, transient response, and distortion levels are directly affected by design choices, highlighting the importance of careful engineering and craftsmanship.
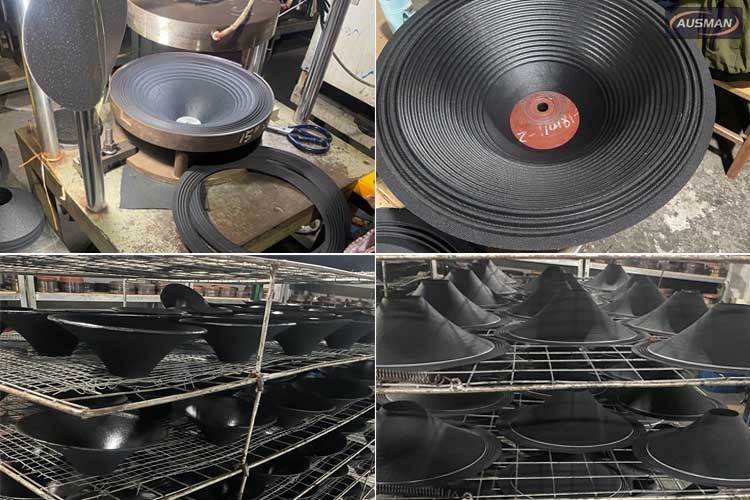
4. Speaker Cone Manufacturing Process
As one of the parts of the speaker manufacturing, the production of speaker cones is also a complex process.
Preparing Raw Materials
The speaker cone manufacturing process begins with the preparation of raw materials.
Various materials are sourced and processed to meet specific requirements for cone production.
Cone Shaping and Molding
Once the raw materials are prepared, they undergo shaping and molding processes to form the desired cone structure.
Advanced molding techniques are employed to achieve precise dimensions and contours.
Treatment and Finishing
After molding, the speaker cones undergo treatment processes to enhance their performance and durability.
This may include treatments to improve rigidity, dampening properties, or resistance to environmental factors. Finishing touches such as coatings or laminates are applied for aesthetics and protection.
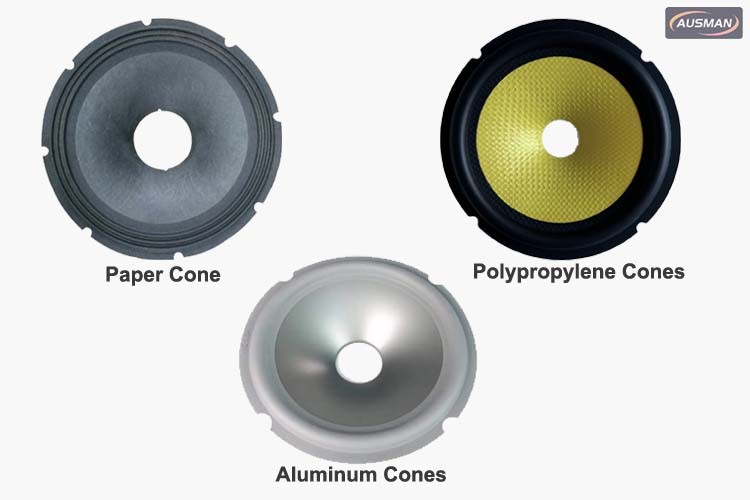
5. Types of Speaker Cone Technologies
Paper Cones
Paper cones offer a traditional sound reproduction with smooth frequency response. They are cost-effective and widely used in various audio applications.
Polypropylene Cones
Polypropylene cones are lightweight and rigid, providing enhanced bass response and durability. They are commonly found in consumer audio systems.
Kevlar Cones
Kevlar cones are known for their exceptional strength-to-weight ratio, offering precise and detailed sound reproduction, particularly in midrange frequencies.
Aluminum Cones
Aluminum cones deliver excellent transient response and high-frequency extension, making them ideal for high-fidelity audio applications.
6. Quality Control in Speaker Cone Production
Just like the Speaker Assembly Processes, the speaker cone also needs to be tested, and only qualified products will move to the next step.
Testing Procedures
Stringent testing procedures are implemented throughout the manufacturing process to ensure that each speaker cone meets quality standards for durability, acoustics, and consistency.
Ensuring Durability and Performance
Quality control measures are crucial for ensuring the durability and performance of speaker cones. Any deviations or defects are identified and rectified to uphold product quality.
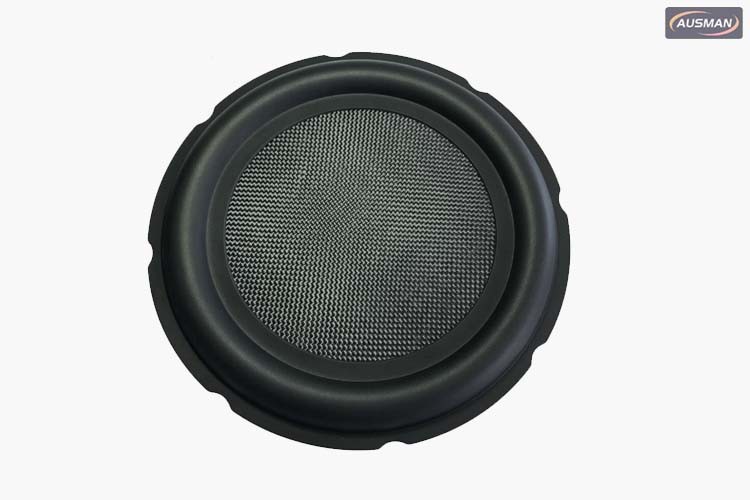
8 Inch Speaker Glass Fiber Cone
7. Innovations in Speaker Cone Manufacturing
Advancements in Materials
Advancements in materials science have led to innovations in speaker cone design.
Manufacturers continue to explore new materials and methods to improve performance, efficiency, and durability.
Novel Manufacturing Techniques
Novel manufacturing techniques such as advanced molding processes and automation have streamlined production and enhanced the precision of speaker cone manufacturing.
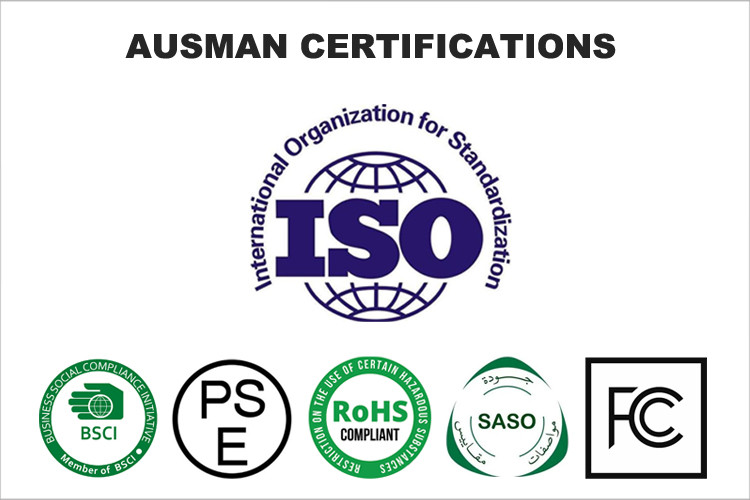
8. Environmental Considerations
Sustainable Materials and Practices
The industry is increasingly adopting sustainable materials and practices to minimize environmental impact.
Recycled materials, biodegradable options, and energy-efficient manufacturing methods are being explored to reduce the ecological footprint of cone production.
Recycling Initiatives in Speaker Cone Production
Recycling initiatives aim to minimize waste and promote responsible disposal practices within the industry.
Manufacturers are investing in recycling programs to recycle materials and reduce the environmental impact of cone production.
9. Challenges and Solutions
Addressing Common Issues in Cone Manufacturing
Despite advancements, cone manufacturing faces challenges such as material limitations, production efficiency, and cost management.
Ongoing research and development efforts are focused on addressing these challenges and driving improvements in the field.
Future Prospects and Improvements
Future prospects for cone manufacturing include advancements in materials, manufacturing techniques, and sustainability practices.
Continued innovation and collaboration within the industry are expected to drive progress and improve the quality of speaker cones.
10. Applications of Speaker Cones
Consumer Audio Systems
Speaker cones find widespread applications in consumer audio systems, from home theaters to car audio.
They play a crucial role in delivering immersive sound experiences for consumers.
Professional Sound Reinforcement
In professional audio setups such as concert venues and recording studios, high-quality speaker cones are essential for accurate sound reproduction and performance.
11. Impact of Speaker Cone Design on Sound Quality
Acoustic Properties of Different Cone Materials
The choice of cone material significantly impacts sound quality and performance. Factors such as frequency response, transient response, and distortion levels are directly influenced by cone material and design.
How Design Affects Frequency Response
Design considerations such as cone shape, size, and construction influence frequency response, affecting the tonal balance and sonic characteristics of speaker cones.
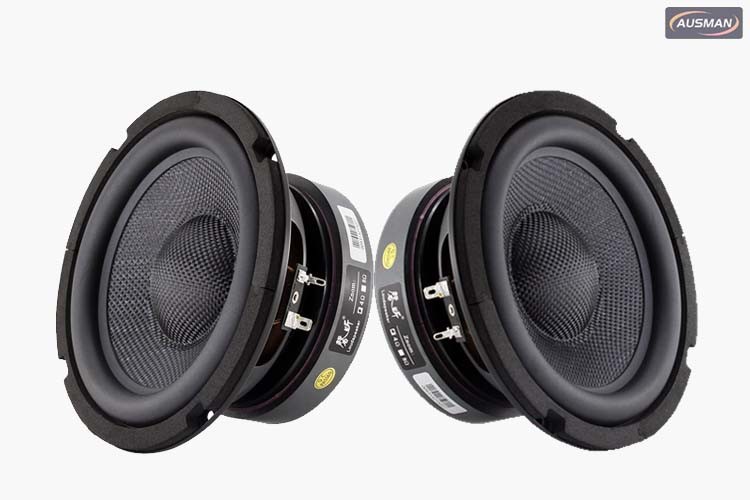
6.5" Galass Fiber Cone Speaker
12. Manufacturers of Speaker Cones
Manufacturers Worldwide
Speaker cones are manufactured by companies worldwide, with notable manufacturers located in regions such as the United States, Europe, and Asia.
For examples: Eminence(United States), Celestion(England), Faital PRO (Italy), Beyma (Spain).
Manufacturers in China
China is a significant hub for speaker cone production, home to numerous manufacturers known for their expertise and innovation in the field.
For examples: Tackcheong, Standish Co., Ltd, Chinaetech.
13. Future Trends in Speaker Cone Manufacturing
Predictions for Upcoming Innovations
Future trends in cone manufacturing include advancements in materials science, smart technologies, and sustainability practices. These innovations are expected to drive progress and shape the future of the industry.
Potential Disruptions in the Industry
Disruptions such as emerging technologies, changing consumer preferences, and regulatory changes could impact the cone manufacturing industry.
Adapting to these disruptions and embracing innovation will be key for staying competitive in the market.
14. Packaging and Shipping of Speaker Cones
Speakers are fragile products and are prone to deformation and damage during transportation, so reasonable packaging design and transportation are crucial.
Packing
Secure Packaging: Each speaker cone should be carefully wrapped and cushioned to prevent any damage during transit.
Customized Solutions: Packaging solutions are tailored to fit different sizes and shapes of speaker cones, ensuring a snug and secure fit.
Shipping
Reliable Shipping Partners: Choose the trusted shipping carriers to ensure timely and reliable delivery of speaker cones to their destinations.
15. Conclusion
Speaker cones are integral components of audio systems, responsible for converting electrical signals into audible sound waves.
Understanding the manufacturing process, key components, and applications of speaker cones is essential for appreciating their importance in sound production.
As technology continues to evolve, innovations in speaker cone manufacturing are expected to drive progress and shape the future of the industry.
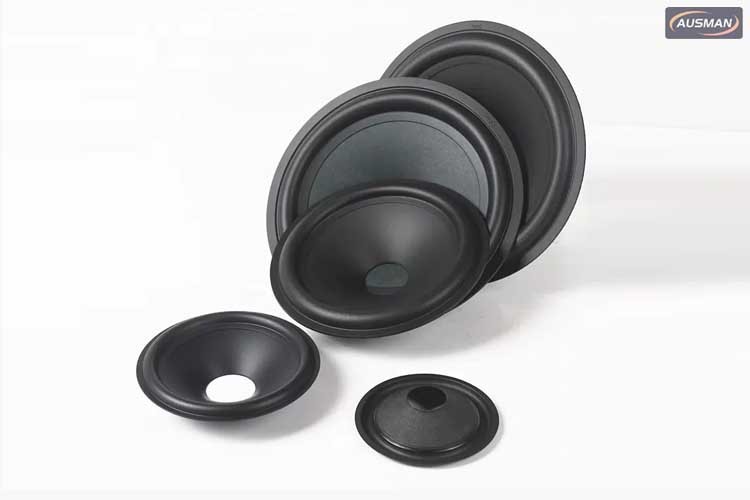
16. FAQs
1. What materials are commonly used in speaker cone manufacturing?
Paper, polypropylene, kevlar, and aluminum are among the most commonly used materials in speaker cone production.
2. How does cone design affect sound quality?
The design of the speaker cone directly impacts sound quality by influencing factors such as frequency response, transient response, and distortion levels. Different cone designs produce varying sonic characteristics, allowing manufacturers to tailor sound reproduction to specific preferences and applications.
3. Are there any eco-friendly options for speaker cones?
Yes, as environmental sustainability becomes increasingly important, manufacturers are exploring eco-friendly materials and production processes for speaker cone manufacturing. Recycled materials, biodegradable options, and energy-efficient manufacturing methods are being adopted to reduce the ecological footprint of cone production.
4. What are the challenges faced in speaker cone production?
Speaker cone production faces challenges such as sourcing high-quality materials, maintaining consistent manufacturing standards, and balancing cost-effectiveness with performance. Additionally, ensuring compatibility with evolving audio technologies and market demands presents ongoing challenges for manufacturers.
5. How can I ensure the longevity of my speaker cones?
Proper maintenance and care are essential for extending the lifespan of speaker cones. Avoiding exposure to extreme temperatures, moisture, and physical damage can help preserve their integrity. Additionally, following manufacturer recommendations for usage and storage can prolong the durability and performance of speaker cones over time.
6. What are the different speaker cone types?
Speaker cones come in various types, including paper cones, polypropylene cones, kevlar cones, and aluminum cones. Each type offers unique sonic characteristics and performance attributes, catering to different audio preferences and applications.
7. Can I replace a damaged speaker cone?
Yes, damaged speaker cones can often be replaced, depending on the extent of the damage and the availability of replacement parts. Replacement cones are available for purchase from manufacturers or third-party suppliers, and professional installation services may be required for proper replacement and calibration.
8. What materials are used in speaker cone construction?
Materials commonly used in speaker cone construction include paper, polypropylene, kevlar, aluminum, and composite materials. Each material offers unique acoustic properties and durability characteristics, allowing manufacturers to tailor cone performance to specific audio requirements.
9. What is the cone of a speaker?
The cone of a speaker refers to the diaphragm component responsible for generating sound waves when driven by an electrical signal. It is typically a cone-shaped structure made of various materials, and its movement creates the vibrations that produce audible sound.
10. What is the price of a speaker cone?
The price of a speaker cone can vary depending on factors such as material quality, size, brand, and manufacturing complexity. Speaker cones are available at a range of price points, from budget-friendly options to high-end models with advanced features.
11. How to repair a speaker cone(speaker cone replacement)?
Repairing a speaker cone may involve techniques such as re-gluing detached portions, patching small tears or punctures, or replacing damaged sections with new material. Specialized adhesives and repair kits designed for speaker cone repair are available, and professional repair services may be necessary for more extensive damage.
12. What is the best material for a speaker cone?
The best material for a speaker cone depends on various factors such as desired sound characteristics, intended application, and budget considerations. Paper cones are known for their natural sound reproduction, while polypropylene and kevlar cones offer enhanced durability and performance. Ultimately, the best material choice depends on individual preferences and audio requirements.
- 1000+ Clients Choose AUSMAN
- Your Ideal OEM/ODM Manufacturer