Polypropylene Speaker Cones: Soft Parts In Speaker Production
Speaker Cone: Paper Cone and Polypropylene(PP) Cone
In the production of speakers, we can understand that their construction mainly includes speaker frames, voice coils, magnets, speaker baskets, cones, etc.
From its invention in the 19th century to today, people have conducted in-depth research on its components, but the topic of "how to improve sound quality" is an ongoing one.
We all know that there are only about a dozen components, but assembling them into a high-quality speaker can be considered an art.
The cone is a soft component, and currently, there are two main types: paper cones and polypropylene cones.
Here, we will introduce the polypropylene speaker cones, including their types, materials, and pros/cons analysis.
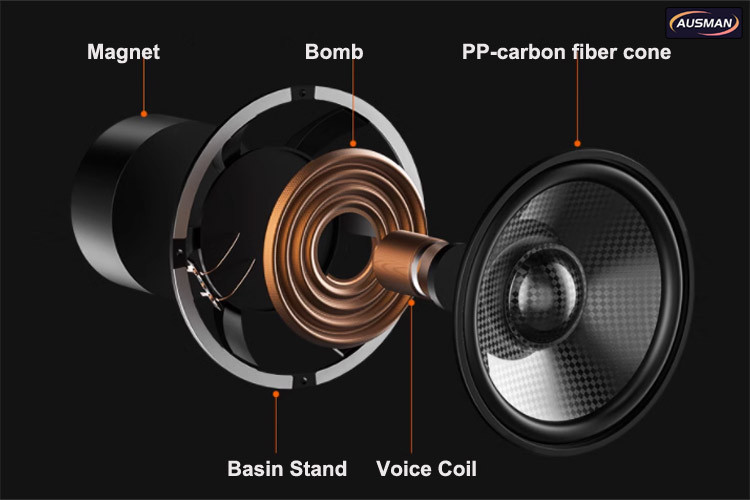
Plastic Speaker Structure
What Is A Polypropylene Speaker Cone
A polypropylene speaker cone is a thin film made from polypropylene material, usually with a circular or elliptical shape. It is used as the vibrating element of a speaker.
When current flows through the speaker's driver unit (including the voice coil and magnet), the cone begins to vibrate, generating sound waves.
It is an essential part of a speaker, generating sound through vibrations and converting electrical signals into auditory signals.
Polypropylene, as a material, has suitable rigidity and damping properties, making it suitable for applications that convert electrical energy into sound energy.
Most of AUSMAN AUDIO products use paper cones.
Types of Polypropylene Speaker(PP) Cones
Because it is a composite material, physical and chemical properties such as rigidity, density, and color can be achieved through formula control.
There are various types and components available in the market to meet different sound qualities, market positioning, and application needs.
The main types are below:
Polypropylene Film
This is a common type, made from pure polypropylene or a composite of polypropylene and other materials. Polypropylene film has moderate rigidity and lightness, suitable for low to mid-frequency vibrations, widely used in home audio, car audio, etc.
Polypropylene Composite
To enhance the characteristics of the diaphragm, polypropylene can be combined with other materials such as cellulose paper, fiberglass, etc. This can improve the rigidity, damping performance, and frequency response of the diaphragm, thus enhancing sound quality.
Polypropylene/Polyester Blend
Polyester is another material commonly used for diaphragms. Mixing it with polypropylene can balance the advantages of both materials and achieve better performance.
Dual-Layer Polypropylene
High-end speakers may use dual-layer polypropylene diaphragms, achieved through different layers of design to achieve more precise vibration and better frequency response.
Polypropylene speaker cones can achieve different acoustic characteristics through single materials or composites. This can meet the needs of specific situations.
Production Process
As a thermoplastic polymer, polypropylene is mainly produced using a thermoplastic molding process. Due to its applicable characteristics, it is widely used in cone manufacturing.
The production process of polypropylene speaker cones involves multiple steps, each of which affects the final design and performance.
First, the manufacturer needs to select high-quality polypropylene pellets, with standards based on characteristics such as stiffness, density, and heat resistance.
Then, the selected polypropylene pellets are melted and injected into molds, which are pre-fabricated and determine the appearance, shape, and characteristics of the cone. Injection molding provides geometric shape and thickness to the cone.
Subsequently, the melted polypropylene is cooled and solidified within the mold. This allows the cone to maintain the desired shape and characteristics, also known as molding.
After solidification and molding, excess material is trimmed, resulting in the final shape and size of the cone.
Additionally, the surface of the cone needs to be treated to improve the adhesion of other materials (such as coatings or adhesives).
Workers will use suitable adhesives to attach the polypropylene cone to the driver unit (voice coil and magnet assembly).
Finally, after passing quality control tests, the speaker meets design specifications and performance standards.
Advantages
Lightweight: Polypropylene's lightweight design can help improve the overall efficiency and response of the speaker.
Moderate Rigidity
The rigidity of the cone enhances its ability to accurately reproduce sound frequencies without distortion.
Inherent Damping
Inherent damping properties help control undesirable resonances, achieving clearer and more accurate sound reproduction.
Moisture Resistance
Polypropylene is inherently resistant to moisture and environmental conditions, extending the cone's lifespan. It surpasses paper cones in this aspect.
Low Cost, High Efficiency
Injection molding is efficient and cost-effective for mass production, albeit with initial mold-making requirements. It excels over paper cones in terms of production efficiency and cost.
Disadvantages
Despite the advantages of polypropylene cones, they may have limitations in reproducing certain high-frequency ranges and their performance may not meet some requirements, necessitating the use of paper cones.
Lack of Rigidity
While it can meet the demands of most situations, the rigidity of polypropylene may not match certain other high-end diaphragm materials, affecting the final audio precision.
Weak in High-Frequency Response
Compared to dedicated materials (such as silk or metal), polypropylene cones may not perform well in reproducing extremely high-frequency ranges.
Aging Issues
When exposed to ultraviolet light, polypropylene cones may experience color fading or degradation, a phenomenon known as aging.
Conclusion
Compared to paper cones, polypropylene speaker cones have advantages in moisture resistance and waterproofing, as they are only mildly affected.
Additionally, as a synthetic material, there are many improvement options, making its applications versatile.
Furthermore, in most cases, it does not require high-end crossovers, effectively controlling the production costs of speakers.
However, it does come with performance drawbacks.
Nonetheless, being cost-effective, suitable for mass production, and applicable to most products, it is a very good option that effectively complements the shortcomings of the paper cone industrial applications.
Get Help For Speaker Import From Supplier AUMSAN Audio China
If you want to know more about speaker manufacturing, please pay attention to our blog update.
Ausman is a supplier of portable party speakers, PA speakers, DJ speakers, retro sounds, etc.
Our wholesale business faces global small and medium -sized brands and wholesalers.
l l Related Reference Resources: